Nos negócios, a competição acontece sempre pelo lucro. Cadeias produtivas, com mais capacidade de adicionar valor, gerando mais lucro, são sempre mais competitivas. Nesse cenário, qualquer desperdício é uma restrição para o sucesso nos negócios e um entrave para a competitividade. Por isso, eles devem ser, sistematicamente, identificados, combatidos e minimizados ou eliminados.
O combate ao desperdício, sistemático e eficiente, fica mais fácil a partir da lista de oito fontes comuns de desperdício, proposta por Taiichi Ohno, um dos pais do Sistema Toyota de Produção.
Oito fontes de desperdício, segundo Taiichi Ohno
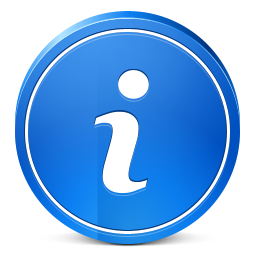
- Produção excessiva – gerando entregas em tempos menores ou em quantidades maiores do que os clientes desejam ou conseguem absorver;
- Estoque superdimensionado – aumentando a necessidade de “capital de giro” com matérias-primas ou produtos acabados;
- Espera – desperdiçando capacidade produtiva das pessoas ou recursos operacionais durante a execução de um processo;
- Movimento – fazendo com que as pessoas se desloquem na planta ou cumpram “pedágios burocráticos” para poderem cumprir suas atividades;
- Transporte – aumentando, em muitos casos, tempos em “espera”, com a transferência de insumos, documentos e trabalho ou equipamentos;
- Trabalho excessivo – geralmente associado a tarefas de verificação ou adição de features que o cliente não valoriza (ou, pelo menos, não está disposto a pagar para ter);
- Subutilização de capacidade – pagando em demasia por máquinas com capacidade produtiva muito acima da demanda, também por “contenção” do talento de pessoas;
- Defeitos – gerando resultados diferente das especificações acordadas.
Todos as fontes de desperdícios listadas por Ohno comprometem a eficiência da operação, reduzem o lucro e tornam as organizações menos competitivas.
***
De todos os desperdícios relacionados por Ohno, o mais evidente são os “Defeitos”. Quando “pegos” antes de chegar aos clientes, geram desgaste interno e retrabalho. Quando chegam, geram desgastes para a marca e, frequentemente, necessidades de retratações.
No mundo ideal, a operação seria plenamente assertiva. Na prática, quanto antes um “Defeito” é identificado, menores são os custos associados e o impacto do desperdício. A identificação de defeitos demanda testes e outros tipos de verificação.
***
[tweet]Todas as tarefas relacionadas a testes e verificações não adicionam valor percebido pelo cliente. Entretanto, reduzem potencialmente os custos decorrentes dos “Defeitos”.[/tweet]
Em desenvolvimento de software, testes automatizados bem-feitos antecipam detecção de defeitos, mitigando prejuízos e aumentando a eficiência operacional.
Veja também
- [TEC] A adoção de testes automatizados de aceitação melhora o alinhamento do time técnico com o negócio
- [TEC] Testes bem feitos adicionam valor. Testes ruins são apenas custo!
***
[tweet]O lead time para a maioria dos processos produtivos é majoritariamente comprometido por tempos em “Espera” e não por trabalho, efetivamente. Por isso, estimativas de esforço geralmente tem pouca relação com prazos reais de entrega.[/tweet] Dessa forma, sempre que utilizadas sob esse argumento, a elaboração de estimativas é, por definição, desperdício, gerando apenas “trabalho excessivo”.
***
Empresas de software, ansiosas por encantar o cliente, acabam desenvolvendo soluções com muito mais features do que o cliente indicou que precisa. Mais grave que o custo desnecessário para o desenvolvimento é a herança da manutenção mais cara. [tweet]Entregar, sistematicamente, mais que o cliente pede e está disposto a pagar inviabiliza o negócio.[/tweet]
***
Dimensionamento mal feito da demanda produtiva faz com que empresas gastem mais do que necessário em equipamentos. Não é raro encontrar plantas com máquinas, em plantas operacionais, operando em menos de 20% de sua capacidade produtiva.
Nos escritórios, é comum encontrar pessoas paradas, em “Espera”, pelo computador. Programadores, também, frequentemente, tem “subutilização de capacidade” por terem de lidar com máquinas lentas.
***
Plantas mal desenhadas levam operários a se deslocarem em demasia para poderem cumprir suas atividades. [tweet]Escritórios mal projetados são “fábricas de interrupções” que fazem com que as pessoas tenham que deixar suas mesas para conseguir trabalhar.[/tweet]
***
A maior parte da ineficiência logística brasileira vem do custo de armazenamento. [tweet]Em desenvolvimento de software, boa parte do custo está associado ao “represamento” de features por processos ineficientes ou implementações mal feitas de Scrum com sprints como bolsões de coisas prontas, paradas, esperando por release.[/tweet]
***
[tweet]Em meio digital, os principais custos de “transporte” estão relacionados a transferência de artefatos. Desde documentos com requisitos, que demoram para chegar a quem implementa, até software pronto que demora para entrar em produção.[/tweet]
***
A identificação dos desperdícios fica mais fácil a partir da prática disciplinada do mapeamento dos fluxos de geração de valor (VSM) da organização. Afinal, a combinação da visão holística dos processos negócio, ponta-a-ponta, com o exame detalhado de cada etapa é ideal para entender motivações e eliminar justificativas rasas para a ineficiência. As oito fontes apontadas por Taiichi Ohno ajudam nesse tipo de iniciativa.